Reform and innovation
Published:
2019-05-23
Reform and innovation
Reform, innovation, breakthrough; quality, tree brand, increase efficiency... The development of China National Heavy Duty Truck Bridge Company has never been as dynamic as it is today.
Since the in-depth development of the "Brand, Quality, Benefit Year" campaign, in the face of the continuous increase in the order plan, Bridge Box Company has released its vitality with reform, stimulated by innovation, and strived to "achieve the quality of customers, meet the expectations of customers, and create glamour quality." "Production and management has shown a "multi-point flowering" situation. From January to March, the quality claim for bicycles of Bridge Box Company decreased by 20.98% year-on-year, the energy consumption of single bridge decreased by 13.8%, and the profit increased by 56% year-on-year. The development of the company has reached a new level of improvement and efficiency.
Cultivate a "zero defect" culture and benefit from quality
Bridge Box Company's eyes are inward and facing the scene, guided by high performance and lean management, to reduce the after-sales failure rate of the products, to improve the process control as a means, to rely on the whole staff, the whole process, and all-round participation in quality management. Dedicated to building the first brand of China's heavy axles.
Comprehensively strengthen preventive quality management, and shift from “after-the-fact control” to “pre-existing prevention”. Through the full use of quality management tools, Bridge Box Company has played the role of 11 special product quality planning teams to conduct in-depth investigation of product quality, process design, production process testing methods, product development process and operation process. From the product development stage, we will focus on eliminating potential quality hazards and realize the transition to preventive quality management.
Strengthen the monitoring of the changes in quality indicators and quality objectives, and implement the "three noes" principle. In order to strengthen process control, Bridge Box Company strictly implements the three non-principles and product quality problems of “no manufacturing, no circulation, no reception”, and stops production system, giving full play to the role of 139 quality gates, self-inspection of employees, and self-assessment of teams. And insist on regular inspection of engineering conditions, special process audit and product site two-level review, and strict control of the process. The production departments have made great efforts to create high-quality products and create excellent results. Among them, the drive axle department adopts the method of binding the construction workers and inspectors to the assembly line product quality, and the performance of the implementation personnel is linked with the process execution rate and quality control level of the assembly line; The team leader of each production line of the bridge department randomly checks the execution process of each process, and checks the size of the components in the process of the inspection team; the main reducer department further monitors the process control, and strengthens the three-level review and management of the ministerial level, division level and team level auditing... According to statistics, the pass rate of self-made Manqiao products in the first quarter of the bridge company was 100%, and the pass rate of the purchased Manbridge products was 100%.
While continuously improving the quality control standards, Bridgebox Company is aiming at quality problems, fully implements 56 “Competition Tables” of company-level quality improvement projects, clarifies responsible persons, time schedules, and comprehensively supervises the organization of special quality research. Among them, the main reducer assembly "thrust bearing replaces the metal gasket" improvement project, the average first fault mileage of the vehicle before the improvement of 5886 km to the current 30,000 to 40,000 km still has no failure of the shaft difference assembly. It is presumed that the improved average first fault mileage is above 50,000 kilometers.
Active change, innovation management
In the face of continuous improvement in production and management, the bridge box company is not pursuing a vigorous momentum, but through reform and innovation, to create a "first brand" with "first quality", and strive to enhance corporate image, influence and competitiveness -
Implement centralized demand, improve input and output accuracy and efficiency of logistics organization, ensure the stability of product quality with stable production beats; revise the “Data and Indicator Management Procedures” and “Work Task Completion Confirmation Form”, etc. At the same time, the work completion situation has increased the content of the system management department, providing effective support for scientific evaluation of the performance of various departments; reforming the salary distribution mechanism, implementing the performance salary of all employees consisting of output, quality and efficiency, reflecting the “dry and dry” Not the same, doing a good job is not the same." All production departments have introduced a new competition mechanism, formulated a product quality warning system, an inspector performance elimination system, and a day-to-day non-performing product system...
Only reform can have a strong driving force to improve quality and efficiency; only innovation can inject a steady stream of momentum for development. In order to create a product with vitality and soul, Bridge Box Company vigorously promotes the product benchmarking system. Especially in the process of new product development, the bridge box company jumped out of the limitations of the old product design, with Manbridge as the benchmark, to improve the AC16, STR, HW bridge and other old products as the goal, improve the standard, lengthen the "short board", so that Each position and each process has a benchmark product. Each first-line team has carried out in-depth development of benchmarking with advanced teams and advanced processes, finding gaps, analyzing reasons, broadening ideas, and innovating methods.
At the same time, in order to encourage employees to actively discover quality problems, Bridge Box Company established a reward mechanism for the first-line personnel to discover problems independently, and rewarded both spiritually and materially. The implementation of the reward and punishment mechanism has greatly enhanced the quality control awareness and responsibility of employees. “We must pay great attention to quality. Now the quality is closely related to our wages. Moreover, there are quality rewards after finding quality problems.” Employees have reflected this.
Up to now, the qualification rate of each process product inspection has reached a historically optimal level.
Keyword:
Related News
Main Products: HOWO-T7H | HOWO, HOWO Dump Truck, HOWO, Golden Prince, HOWO a7, HOWO Quotation;
Address: Dangjiazhuang Dougou Heavy Truck Four Reservoir Industrial Park, Shizhong District, Jinan City (China Heavy Truck First Start Zone)
Focus on us
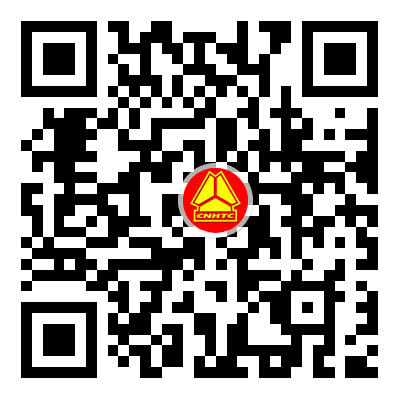